Produktion
Das internationale, markenübergreifende Produktionsnetzwerk ermöglicht den Prozess vom Lieferanten zur Fabrik und zur Montagelinie sowie von der Fabrik zum Handel und zum Kunden. Voraussetzung für unsere Wettbewerbsfähigkeit ist eine dauerhafte Effizienz. Um den Herausforderungen der Zukunft begegnen zu können, setzen wir auf ganzheitliche Optimierungen, zukunftsgerichtete Innovationen, flexible Lieferströme und Strukturen sowie eine agile Mannschaft. Im Geschäftsjahr 2020 lag die weltweite Fahrzeugfertigung mit 8,9 Mio. Fahrzeugen um 17,8 % unter dem Vorjahreswert. Dies resultierte überwiegend aus der weltweiten Ausbreitung des Coronavirus SARS-CoV-2 und den damit verbundenen Maßnahmen zur Eindämmung der Pandemie wie beispielsweise kurzzeitige Schließungen der Fabriken oder Produktionskürzungen insbesondere im ersten Halbjahr 2020 aufgrund von Unterbrechungen der Lieferketten, der Logistik oder Schließungen der Handelsbetriebe. Trotz anhaltend schwieriger Rahmenbedingungen in vielen Märkten, konnte die Produktion im zweiten Halbjahr 2020 annähernd auf Vorjahresniveau stabilisiert werden. Um die Fertigungsprozesse unter Pandemie-Bedingungen aufrecht zu erhalten und unsere Belegschaft zu schützen, haben wir im Rahmen unserer Safe-Production-Initiative Verhaltensweisen und Maßnahmen zur Vermeidung möglicher Infektionsketten zwischen den handelnden Personen im Netzwerk erarbeitet und verabschiedet. Dazu zählen im Wesentlichen Regelungen zur Pflicht zum Tragen von Mund-Nasen-Schutzmasken, das Einhalten von Verhaltensregeln insbesondere Abstandsregeln, Hygienevorschriften und Lüftungszeiten sowie das Umgestalten der Schichtmodelle und Pausentaktungen. Wir überprüfen die formulierten Maßnahmen zur Eindämmung der Covid-19-Pandemie kontinuierlich und passen diese bei Bedarf an.
Die Produktivität nahm im Vergleich zum Vorjahr um 0,8 % zu.
Produktionsstrategie „Intelligent vernetzt“
Die Produktion unterstützt die Konzernstrategie TOGETHER 2025+ mit ihrer Funktionalbereichsstrategie „Intelligent vernetzt“. Durch die intelligente Vernetzung von Menschen, Marken und Maschinen wollen wir die Kräfte und Potenziale unserer weltweiten Fertigung und Logistik bündeln und dadurch Synergien erschließen. Die Leitplanken sind unsere vier strategischen Zielfelder:
- Wandlungsfähiges Produktionsnetzwerk
- Effiziente Produktion
- Intelligente Produktionsprozesse
- Zukunftsfähige Produktionsarbeit
Mit markenübergreifenden Initiativen haben wir inhaltliche Cluster gebildet, in denen kompetenzstarke Teams die für die Produktion im Konzern relevanten strategischen Themen bearbeiten. Die wettbewerbsfähige Gestaltung unseres weltweiten Produktionsnetzwerks, die Reduzierung und der Ausgleich von Umweltbelastungen entlang des Produktionsprozesses sind ebenso Beispiele wie die Digitalisierung mit ihren Auswirkungen auf Produktions- und Arbeitsprozesse sowie auf die Zusammenarbeit. Ein szenarienbasierter Strategieprozess wurde im Zuge der Tranformationsphase in der Produktion entwickelt, der sich an einem Betrachtungszeitraum bis 2040 orientiert. Übergreifendes Ziel ist es, die Produktivität und die Profitabilität zu steigern. Wir wollen die Wettbewerbsfähigkeit unserer Standorte mit einer optimalen Auslastung unserer Fabriken sicherstellen und so Produkte mit hoher Qualität und hohem Kundennutzen zu wettbewerbsfähigen Kosten fertigen.
Globales Produktionsnetzwerk
Das Produktionsnetzwerk des Konzerns erstreckt sich über zwölf Marken und 118 Produktionsstandorte einschließlich unserer chinesischen Joint Ventures. Eine Standardisierung der Produktion mit einheitlichen Produktkonzepten, Anlagen, Betriebsmitteln und Fertigungsprozessen ist ein wesentlicher Faktor unserer zukunftsorientierten Fertigung. Wir entwickeln unsere Produktionskonzepte stetig weiter, richten sie auf neue Technologien aus und wollen dabei ambitionierte Ziele in den einzelnen Projekten realisieren.
Die flexiblen Produktionskapazitäten auf Basis unserer Plattformen bieten die Möglichkeit, Synergien zu heben, auf Marktanforderungen zu reagieren, das Produktionsnetzwerk bedarfsgerecht auszulasten sowie Mehrmarkenstandorte zu realisieren. Aktuell sind bereits knapp die Hälfte der 47 Pkw-Standorte Mehrmarkenstandorte. Das Musterbeispiel im Konzern bleibt weiterhin der Standort Bratislava: Hier werden Fahrzeuge der Marken Volkswagen Pkw, Audi, Porsche, SEAT und ŠKODA produziert.
Der Volkswagen Konzern hat sich zum Ziel gesetzt, bis 2025 ein weltweit führender Anbieter batterieelektrischer Fahrzeuge zu werden. Grundlage hierfür ist die Einführung des Modularen E-Antriebs-Baukastens (MEB). Mit ihm ergänzen wir unser Angebotsportfolio um weitere batterieelektrische Fahrzeuge. Seit 2019 werden in Zwickau, dem ersten Elektrostandort des Volkswagen Konzerns, batterieelektrische Fahrzeuge, wie beispielsweise der ID.3 der Marke Volkswagen Pkw, auf Basis des MEB gefertigt. Im Jahr 2020 wurde das
Portfolio der MEB-Plattform in Zwickau durch den ID.4 der Marke Volkswagen Pkw sowie durch den Enyaq iV der Marke ŠKODA am Standort Mlada Boleslav erweitert.
Um Mehrmarkenprojekte und Elektromobilität in Verbindung mit bestehenden Konzepten wirtschaftlich zu gestalten, ist es erforderlich, die Fertigung flexibel und effizient auszurichten. Außerdem ist die maximale Nutzung von Synergiepotenzialen ein entscheidender Faktor für den Erfolg künftiger Fahrzeugprojekte. Der Einsatz von gleichen Teilen, Konzepten sowie Fertigungsprozessen ermöglicht die Reduzierung von Investitionen und die Chance, vorhandene Kapazitäten besser auslasten zu können. Zukünftig werden elektrifizierte Fahrzeugprojekte an Mehrmarkenstandorten wie zum Beispiel in Hannover hinzukommen.
Produktionsstandorte
Nach dem Verkauf von Renk umfasst das Produktionsnetzwerk des Volkswagen Konzerns inklusive unserer chinesischen Joint Ventures nun 118 Standorte, an denen Pkw, Nutzfahrzeuge und Motorräder sowie Aggregate und Komponenten gefertigt werden.
Mit 66 Standorten bleibt Europa unsere wichtigste Produktionsregion für die Fertigung von Fahrzeugen und Komponenten. Allein in Deutschland befinden sich 24 Standorte. In der Region Asien-Pazifik ist der Konzern mit 34 Standorten vertreten, in Nordamerika sind es fünf, in Südamerika neun und in Afrika vier Standorte.
Trotz erschwerter Rahmenbedingungen durch die Auswirkungen der Covid-19-Pandemie haben wir im Berichtsjahr 81 Produktionsanläufe durchgeführt, davon waren 33 neue Produkte beziehungsweise Produktnachfolger sowie 48 Produktaufwertungen oder Derivate.
FAHRZEUGPRODUKTIONSSTANDORTE DES VOLKSWAGEN KONZERNS
Anteil an der Gesamtproduktion 2020 in Prozent
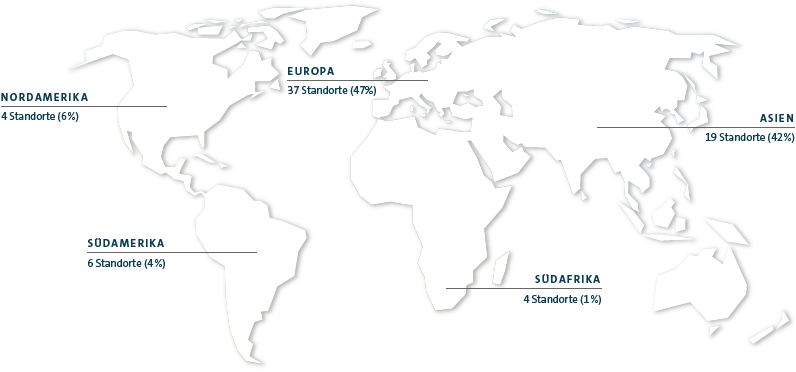
Das Konzern-Produktionssystem
Das Konzern-Produktionssystem stellt uns Methoden und Tools bereit, die die Abläufe an allen Standorten der Marken und Regionen in der Produktion und den produktionsnahen Bereichen kontinuierlich und nachhaltig verbessern sollen. Bei der Weiterentwicklung der Methoden beziehen wir neue Themen und anhaltende Trends mit ein. Schwerpunkte sind unter anderem die Digitalisierung und der Umstieg auf die Elektromobilität. Speziell die Digitalisierung eröffnet neue Anwendungsgebiete, zum Beispiel durch die Nutzung digitaler Daten und Modelle. Daneben bietet die Digitalisierung auch die Möglichkeit, bestehende Methoden in digitale Formate zu überführen und neue, IT-gestützte Werkzeuge zu schaffen. So nutzen wir die Chancen der Digitalisierung und setzen digitale Formate und digitale Tools auch verstärkt in Trainings und Workshops ein.
Bei der Verankerung des Produktionssystems kommt den Menschen im Unternehmen eine zentrale Rolle zu. Wir fördern eine Kultur des wertschätzenden Umgangs miteinander, unabdingbar sind dabei die Themen Führung und Verantwortung des Einzelnen.
Neue Technologien und Digitalisierung
Der 3-D-Druck ist nach wie vor eine der Schlüsseltechnologien von Industrie 4.0 und der Digitalisierung der automobilen Wertschöpfungskette. Die auch als additive Fertigung bezeichneten Technologien werden in nahezu allen Standorten des Volkswagen Konzerns sowohl für die Bauteil- als auch für die Betriebsmittelherstellung erfolgreich eingesetzt. Sie eröffnen in den Bereichen Entwicklung, Design, Produktion und After Sales völlig neue Möglichkeiten. Aufgrund des digitalen Charakters des 3-D-Drucks, der keinerlei Werkzeuge benötigt, lassen sich Bauteile und Betriebsmittel flexibel und direkt aus digitalen Zeichnungen umsetzen sowie gänzlich neue Designs und Bauteilgeometrien verwirklichen. Entwicklungen in Richtung Großserienanwendungen im Automobilbau lassen für die Zukunft erhebliche Potenziale erkennen. Volkswagen nutzt hier durch die enge Zusammenarbeit seiner Marken die Vielfalt des Konzerns und arbeitet mit führenden Technologieanbietern und Forschungseinrichtungen zusammen.
Augmented Reality verknüpft die virtuelle mit der physischen Welt und spielt als gereifte Technologie ebenfalls eine wesentliche Rolle in der Digitalisierung der Wertschöpfungskette – nicht zuletzt aufgrund anhaltender Kontakt- und Reisebeschränkungen durch die Covid-19-Pandemie. Potenziale zur Erhöhung von Effizienz und Innovationsfähigkeit bestehen hier unter anderem im Bereich Remote Support, bei Mitarbeiterschulungen, in der Qualitätssicherung sowie im Entwicklungsprozess. Neben der Implementierung neuer Lösungen, die Datenbrillen, Tablets oder Projektoren als Ausgabemedium nutzen, werden bestehende Augmented-Reality-Anwendungen kontinuierlich auf weitere Standorte des Konzerns ausgerollt.
Grundlage für die Digitalisierung des Produktionssystems ist häufig, Produktionsdaten nutzbar zu machen. Ein Schwerpunkt ist die Nutzung von künstlicher Intelligenz bei Bilddaten, das sogenannte „Industrial Computer Vision“. Hier hat der Volkswagen Konzern eine eigene Plattform für die Umsetzung von konkreten Projekten entwickelt und rollt Anwendungen über seine Marken und Standorte aus. Beispiele dafür sind die Korrektheitsprüfung von Fahrzeugschildern oder die Risserkennung im Presswerk.
Neben den neuen Technologien ist in den nächsten Jahren die Umstellung der IT-Architektur auf eine cloudbasierte Plattformlösung die Kernaufgabe auf dem Weg zur digitalisierten Fertigung. Der Volkswagen Konzern entwickelt hierfür unter anderem die Industrial Cloud in Zusammenarbeit mit Amazon Web Services und dem Integrationspartner Siemens. Die cloudbasierte Plattform mit ihrem vereinfachten Datenaustausch ist eine entscheidende Voraussetzung, um Innovationen schnell und standortübergreifend bereitzustellen. Beispiele sind intelligente Robotik, verbundene Inline-Messsysteme, durchgängige Qualitätsregelkreise, Predictive Maintenance-Anwendungen oder Funktionen der Datenanalytik, um werksübergreifende Prozesse zu analysieren und zu vergleichen. Neue Anwendungen können mit der cloudbasierten Plattform direkt auf alle Standorte skaliert und zentral betrieben werden. Die Umsetzung des Gesamtprojekts ist auf mehrere Jahre ausgelegt. Des Weiteren legt Volkswagen seine Industrial Cloud als offene Plattform an mit dem Ziel, neben den eigenen Standorten auch Unternehmen aus der gesamten Wertschöpfungskette zu integrieren. Langfristig geht es um die Integration der globalen Lieferkette des Volkswagen Konzerns: über 30.000 Standorte von Zulieferern und Partnerunternehmen. So entsteht ein stetig wachsendes, weltweites Ökosystem.
Um zukünftige Innovationen und neue Geschäftsmodelle entlang der gesamten Wertschöpfungskette zu identifizieren, ermöglichen wir mit unserem Open-Innovation-Ansatz den Zustrom an innovativen Ideen und Technologien von externen Start-ups und treiben so zukunftsweisende Innovationen für unsere Produkte, Dienstleistungen und Prozesse innerhalb des Volkswagen Konzerns voran.
GoTOzero Impact Factory
Mit der Funktionalbereichsstrategie „Intelligent vernetzt“ planen wir die Produktion von morgen. Ressourceneinsatz und Emissionen der Standorte des Volkswagen Konzerns erfordern dabei besondere Aufmerksamkeit. Das Programm „goTOzero Impact Factory“ entwickelt konkrete Schritte zu einer nachhaltigeren Produktion. Die Vision dahinter ist eine Fabrik ohne negative Auswirkungen auf die Umwelt.
Wir haben eine Checkliste entwickelt, die die Standorte unterstützt, ihren Status auf dem Weg zu einer „Zero Impact Factory“ zu bestimmen. Diese umfasst derzeit 140 Umweltkriterien und bietet damit die Basis für die kontinuierliche Reduzierung von beispielsweise Energieverbrauch und CO2-Ausstoß.
Um derartige Programme umzusetzen, wird in allen Produktionsstandorten weltweit ein neues Managementsystem eingeführt, das die wesentlichen Themen aus dem Bereich Compliance mit dem Umweltmanagement verknüpft. Dieses Umwelt-Compliance-Managementsystem bildet beispielsweise im Rahmen der Produktionsprozesse die feste Grundlage für die Einhaltung aller externen und internen Regeln in Bezug auf die Umwelt.
Um Synergien zu heben, fördern wir weltweit die Vernetzung und den Austausch zwischen den Marken. Unsere Umweltexperten treffen sich regelmäßig in Arbeitsgruppen. Außerdem schulen wir Mitarbeiter zum Thema Umweltschutz.
In einem IT-gestützten System erfassen und katalogisieren wir Umweltmaßnahmen, die wir für einen konzernweiten Best-Practice-Austausch zur Verfügung stellen. Im Berichtsjahr wurden in diesem System rund 1.520 umgesetzte Maßnahmen im Bereich Umwelt und Energie dokumentiert, die der Verbesserung der Infrastruktur und der Produktionsprozesse von Pkw und leichten Nutzfahrzeugen dienen und beispielsweise in den Dekarbonisierungsindex (DKI) einfließen. Diese Aktivitäten lohnen sich in ökologischer und oft auch ökonomischer Hinsicht und haben einen positiven Einfluss auf die Umweltindikatoren des Konzerns.
GoTOzero Impact Logistics
Die Logistik von Konzern und Marken unterstützt in der gemeinsamen Initiative „goTOzero Impact Logistics“ das Erreichen der Ziele des Umweltleitbildes goTOzero. Das kontinuierliche Optimieren des Transportnetzwerks und der Logistikprozesse reduziert Emissionen – auch mit den Mitteln der Digitalisierung. Darüber hinaus wird stetig der Einsatz neuer, emissionsarmer Technologien im Transport von Produktionsmaterialien und Fahrzeugen geprüft und forciert.
Die vom Volkswagen Konzern ergriffenen Maßnahmen für eine zukünftig CO2-neutrale Logistik umfassen beispielsweise die Verlagerung von Transporten von der Straße auf die Schiene und die nahezu vollständige CO2-Vermeidung durch den Einsatz von Grünstrom im Schienenverkehr in Deutschland in Zusammenarbeit mit der Deutsche Bahn AG.
Weitere Beispiele für die Nutzung der Bahn als emissionsarmer Verkehrsträger sind der Transport der Batteriemodule vom Lieferanten im polnischen Wrocław nach Braunschweig sowie der Transport von Batteriesystemen vom Komponentenstandort Braunschweig in das Werk Zwickau, zur Produktion rein batterieelektrischer Fahrzeuge.
Darüber hinaus nutzt die Konzern-Logistik die weltweit ersten beiden mit schadstoffarmem Flüssigerdgas (LNG) betriebenen Roll-on-Roll-off (RoRo)-Charterschiffe für den Fahrzeugtransport über den Nordatlantik.